Injection Molding Capabilities
HTP operates 25 injection molding machines with clamping forces ranging from 25 to 1,350 tons. Our equipment includes 2-component molding machines and a foil cell with a laminar flow box for producing high-gloss black FIM (Film Insert Molding) parts.
Surface Finishing Expertise
HTP excels in surface finishing, with three paint shops: two robotic and one flatbed painting machine. These facilities are primarily used for applying haptic decorative lacquers, such as soft-touch finishes, and high-gloss black coatings. Our goal is to offer a wide range of surface finishes to meet the diverse needs of the automotive interior industry.
Comprehensive Assembly Services
HTP provides full assembly services for plastic parts and pre-assemblies. Our assembly lines handle tasks such as attaching clips or welding components onto carrier parts using e.g. ultrasonic welding. Every finished part goes through a final quality check to ensure it meets customer requirements.
Premium Automotive Interior Parts
Our products are mainly used in premium car interiors, including center consoles, instrument panels, and door panels. These parts must meet high standards for both tactile and visual quality. Technical requirements, such as scratch resistance for high-gloss black surfaces, are achieved usingUV-hardening lacquers or FIM foils with UV hard coats.
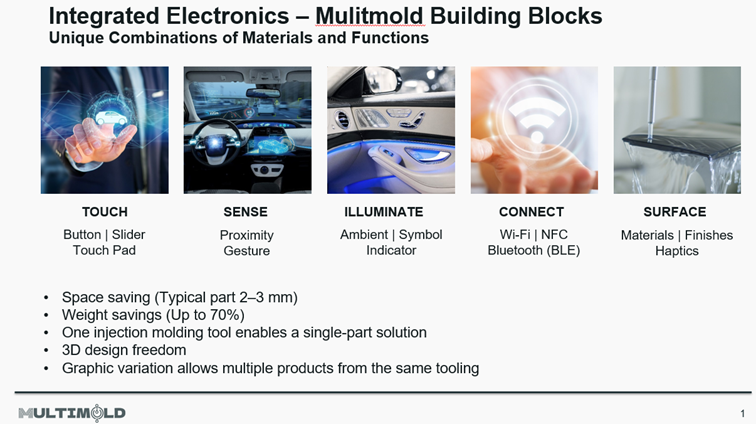
Innovations in In-Mold Technology
In the Multimold project, HTP focuses on advanced in-mold electronics. We have experience in overmolding 3D-formed foils with printed circuits, addressing challenges like integrating electronic components onto foils before overmolding. This technology is crucial for creating sophisticated electronic parts for automotive applications.
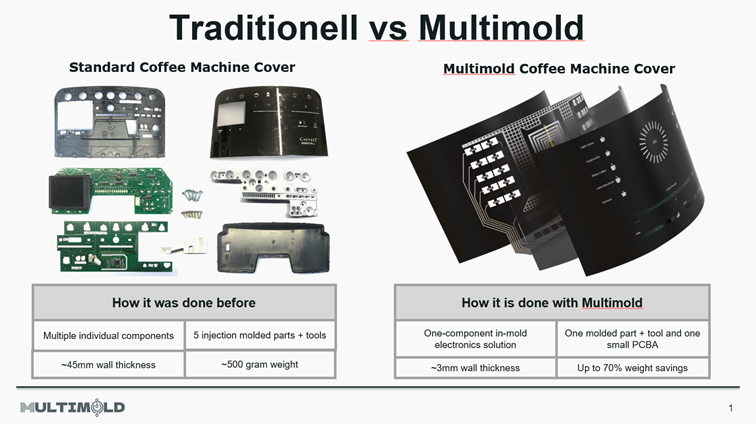
Ensuring Process Stability
As a serial manufacturer, HTP prioritizes process stability to gain acceptance from automotive customers. Stable processes are essential for introducing new technologies. We invest significant effort to ensure machine capability, minimize defects, maintain production availability and checking each step in the process chain.
Collaborative Efforts in the Multimold Project
HTP benefits from the expertise of various professionals involved in the Multimold project. The process begins with Moldflow analysis, enhanced by input from Montanuniversität Leoben, to improve process planning and achievebetter results in molding operations. Optimized Moldflow simulations, especially for foils with printed electronics and assembled components, help translate theoretical models into physical parts.
Advancements with PyzoFlex® Sensors
The Multimold project also explores the use of printed PyzoFlex® sensors in overmolding. These sensors are investigated for their behavior during the injection molding process. PyzoFlex® sensors offer an alternative to traditional capacitive touch sensors in car interiors, reducing interference and creating more stable HMI (Human-Machine Interface) systems. This innovation is particularly appealing to customers seeking robust solutions for automotive interiors and other products.
Broader Applications
While our primary focus is on the automotive industry, HTP’s technologies and expertise extend to other sectors including home appliances, leisure, medical, and various mobility solutions. Our advanced molding, finishing, and assembly processes, as well as our innovations in in-mold technology and sensor integration, provide significant benefits across these industries. We aim to improve efficiency, quality, and functionality, there by contributing to advancements in various fields.
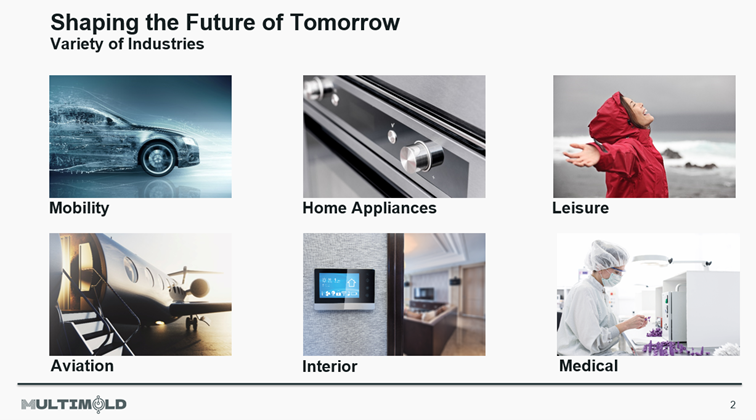