On 11 and 12 June, Multimold partners reunited at the Fraunhofer Institute IVV in Freising - Germany, for the first time after the project’s kick-off meeting. Our partners are working hard to meet the target of the 1st GEN demonstration by the end of 2025 and provide advanced technologies for the production of complex products with the in-mold electronic (IME) processes.
The event was an opportunity to visit the Fraunhofer Institute labs and experience the recycling process behind Multimold.
Testing the 1st GEN demonstrations
The Multimold project can claim well–known and credible partners from the different fields of the manufacturing and research sector that decided to cooperate to develop new high-quality products based on IME.
During the meeting, we shared the progress achieved in the first prototype tests and the first challenges we encountered on the way towards the further development of the IME technology.
For the industrial sector, our goal is to design an integrated solution for the operator interfaces using IME. First forming tests have been conducted to select the most appropriate design to achieve our ambition.
For the automotive and wind turbine sectors, we conducted some injection mold simulations to test the prototypes and we already tested materials to allow the overmolding of sensitive electronics.
Sustainability as a priority: working for a circular-by-design product
Along with the innovation development, our goal in Multimold is to offer the market some molded products that will be easily recyclable and that the physical debonding of electronic and plastic materials present in the products. In this period, we worked on the first experiments for the plastic materials’ recycling in order to make the automotive sector more sustainable.
We also visited the Fraunhofer Institute laboratories where the process of reducing plastic objects into re-usable materials to produce new products happens. Starting from this process, we aim to make this process possible for over-molded products to create new ones.
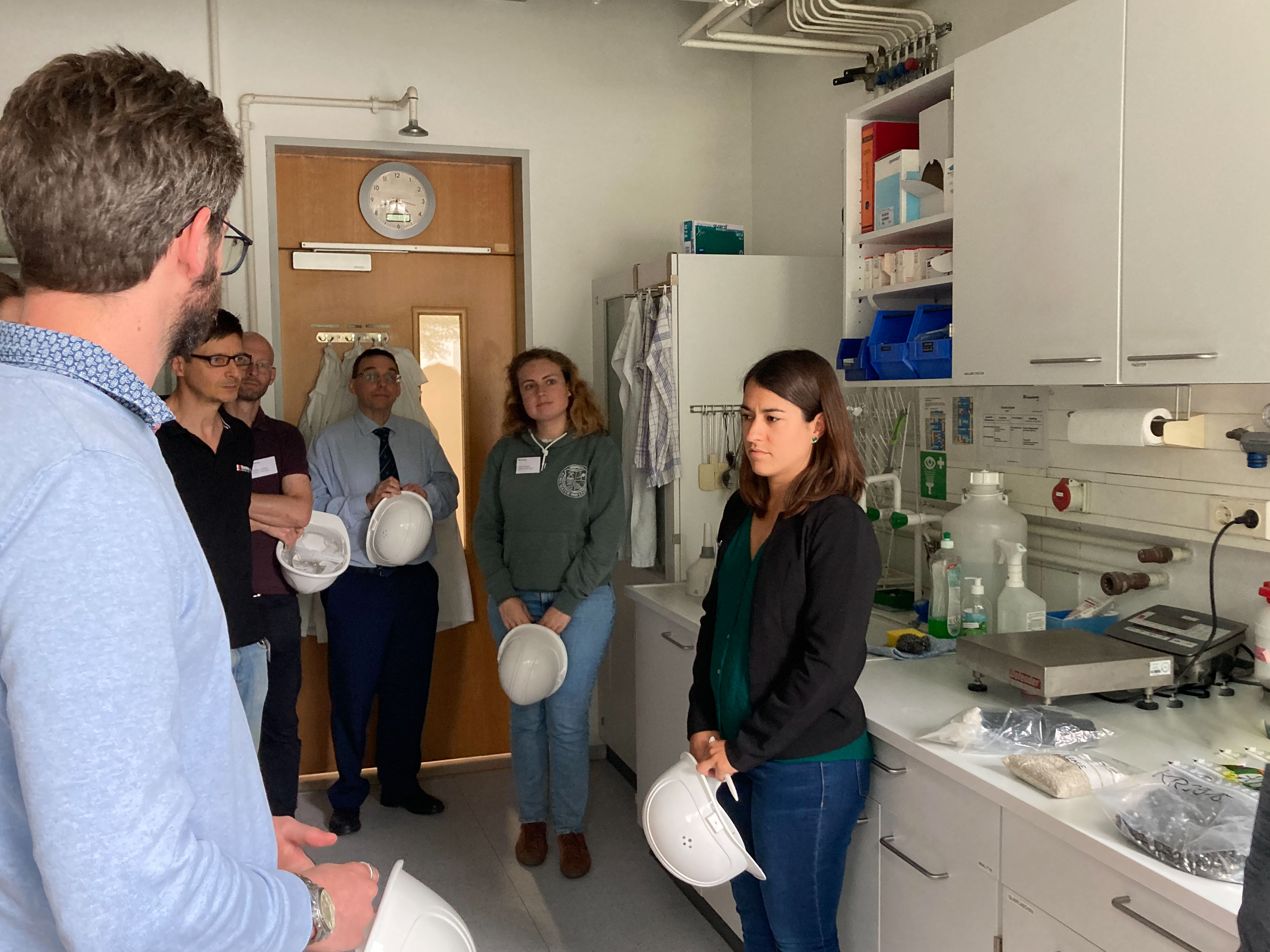
Together with the debonding technologies, our project will improve the Life Cycle Assessment of the prototypes developed and indicate the environmental impacts and benefits of the products.
This meeting was fruitful in moving forward our research and it showed we are on the right track.
Follow our project and keep updated on the progress of the injection molding.